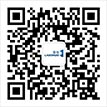
2020 官網升級中!現在您訪問官網的瀏覽器設備分辨率寬度低于1280px請使用高分辨率寬度訪問。
3D printing technology is rapidly changing the traditional way of production and life. In just 30 years, 3D printing technology has achieved rapid development and attracted wide attention from all over the world. With the continuous improvement of the maturity and performance of 3D printing technology, the materials used in 3D printing are more and more widely, especially metal materials. We know that SLM technology and SLS technology are the mainstream metal parts printing technology, so how are they different?
In 1989, C. Deckard of The University of Texas proposed laser selective sintering (SLS) technology, and later established DTM Company. In 1995, the Fraunhofer Laser Institute in Germany proposed laser selective melting (SLM) technology, which can directly form nearly completely dense metal parts. SLM and SLS are powder printing technology, and the printing process is basically the same. Print shop spread powder by car before the start of the powder material to print platform, again by laser sintering or melting, and realization of a layer of print, on each layer, forming platform would fall by a thick layer of height, then spread powder cartridge back, again by the laser thermal forming, one layer stacked to form a three-dimensional parts, to prevent the oxidation of the metal, The whole process needs to take place in an inert gas environment.
SLM成型原理圖
SLS成型原理圖
Although the principle of the two technologies is the use of the thermal effect of the laser beam, but SLM and SLS laser target is different, they use different lasers. In order to better melt metal, SLM technology needs to use laser beam with high absorption rate of metal, so generally used nD-YAG laser (1.064 micron) and fiber laser (1.09 micron) laser beam with short wavelength. SLS technology is generally used for CO2 lasers with long wavelengths (9.2-10.8 microns).
SLM technology prints metal
SLM technology uses lasers to heat metal powder directly to melt it completely and then cool it to form. SLM is a promising 3D printing technology for metal parts. SLM molding materials are mostly single component metal powder, including austenitic stainless steel, nickel base alloy, titanium base alloy, cobalt-chromium alloy and precious metals, etc. Laser beam can quickly melt metal powder and obtain continuous molten channel, which can directly obtain almost any shape, complete metallurgical bonding, high precision and nearly compact metal parts.
Metal parts printed using SLM technology
SLS technology prints metal
Single metal powder sintering
Sintering of a single metal powder: for example, iron powder is preheated to a certain temperature and then scanned and sintered with a laser beam. After hot isostatic pressing, the relative density of sintered parts can reach 99.9%.
Metal mixed powder sintering
Sintering of metal mixed powder: Mainly a mixed powder of two metals, one of which has a lower melting point and the other has a higher melting point. For example, a mixture of bronze and nickel powder. The metal mixture powder is preheated to a certain temperature. A laser beam is then scanned to melt a metal powder with a low melting point, such as bronze powder, thus binding the refractory nickel powder together. After liquid phase sintering, the relative density of the finished product can reach 82%.
A mixture of metal powder and organic binder powder
Metal parts printed using SLS technology
In addition, the laser sintering process with heating or metal plate heat tube, heat the powder material beyond crystallization temperature, probably about 170 degrees Celsius, molten material are used to realize bond forming, so entities porosity, mechanical performance is poor, parts to use pass high temperature remelting. SLM is laser melt district, as the name implies, that is, in the process of machining using laser melt powder completely, does not need adhesives, forming precision and mechanical properties are better than SLS, because there is no thermal field SLM, however, it needs to be metal flows from the normal temperature of 20 ℃ heated to melting point, the process need to consume a huge amount of energy.